OTIF Complete Guide: How To Calculate, Track, and More
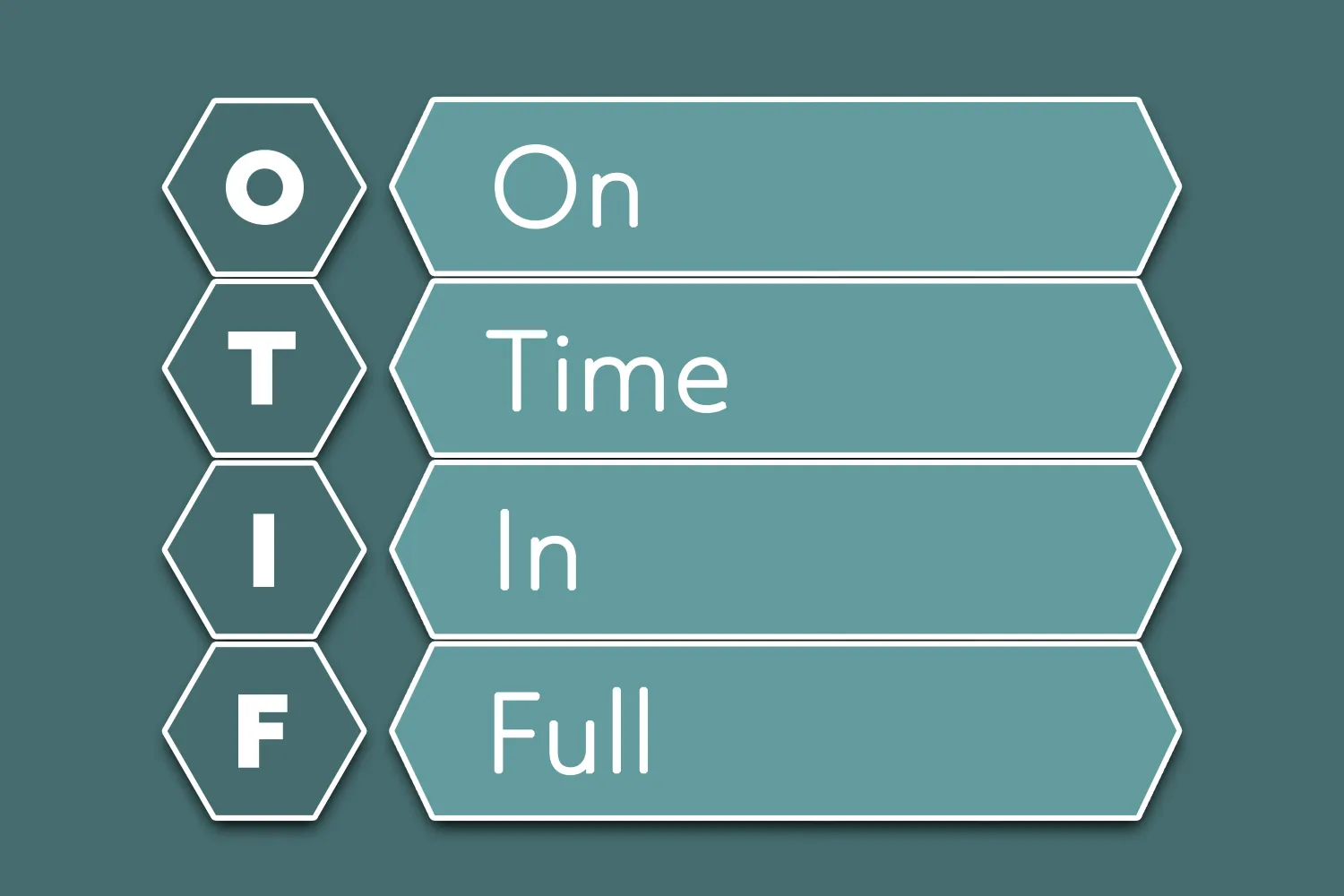
Meeting delivery expectations is essential for success in fast-paced logistics and supply chain management. At Cabrella, we believe On-Time In-Full (OTIF) performance plays a crucial role in ensuring seamless operations and heightened customer satisfaction.
This guide will discuss the nuances of OTIF: what it is, why it matters, and how it can be calculated and optimized to bolster your business. Whether you're a seasoned operator or new to the field, mastering OTIF will help you gain a competitive edge.
What Is OTIF (On-Time In-Full)?
OTIF, which stands for On-Time In-Full, is a key performance indicator in supply chain management that measures the efficiency and accuracy of your shipping and inventory fulfillment operations.
Specifically, it assesses whether goods are arriving at their destination:
- On-Time: Goods must arrive by the date promised to the customer.
- In-Full: Orders must be complete, with all items delivered as specified.
This metric is crucial for analyzing the efficacy of your logistics, pinpointing improvement areas, and ultimately, improving customer satisfaction by meeting their expectations for timely and complete deliveries.
Why Is OTIF Important in Supply Chain Management?
OTIF is central to the operational health of any business involved in inventory and distribution. There are numerous reasons why maintaining high OTIF scores is crucial for enhancing your supply chain efficiency.
- Customer Satisfaction: Delivering orders on time and in full directly impacts customer happiness and trust, leading to repeat business and positive word-of-mouth.
- Reduced Costs: Higher OTIF rates often mean fewer expedited shipments and less need to split orders to fulfill requirements, which saves on shipping costs.
- Inventory Management: Effective OTIF tracking helps businesses optimize their inventory levels, reducing costly stockouts or overstocking.
- Performance Benchmarking: OTIF serves as a benchmark to measure the reliability and efficiency of your supply chain operations against industry standards or competitors.
- Supply Chain Visibility: Regular monitoring of OTIF rates can provide deeper insights into the logistics network, identifying potential bottlenecks or inefficiencies in the supply chain.
- Vendor Regulations: OTIF helps retailers follow vendor requirements, as failing to meet their standards can result in fines or other penalties.
By improving OTIF performance, businesses can streamline their operations, enhance customer service, and ultimately drive growth.
How To Calculate OTIF for Your Business
Calculating OTIF delivery performance is relatively straightforward but requires consistent tracking of shipment and delivery data.
First and foremost, remember that OTIF is a combination of two metrics: "On-Time" and "In-Full." To compute OTIF, you must evaluate both of these aspects.
Calculate the "On-Time" Percentage
Businesses must measure the frequency of their deliveries arriving on the promised date. Divide the number of on-time deliveries by the total number of deliveries, then multiply the result by 100.
For instance, if out of 100 shipments, 95 arrived on time, your "On-Time" percentage is 95%.
Calculate the "In-Full" Percentage
This involves determining how often your orders have been entirely fulfilled without missing any items. Divide the number of complete orders by the total number of orders, then multiply the result by 100.
If, for example, you had 100 orders, and 98 were perfectly fulfilled, your "In-Full" percentage is 98%.
Calculate the Overall OTIF Rate
Now, combine these two calculations. Multiply the "On-Time" percentage by the "In-Full" percentage.
Taking the previous examples, where "On-Time" is 95% and "In-Full" is 98%, the OTIF would be 0.95 * 0.98 = 0.931 or 93.1%.
You have now calculated your OTIF score. The goal is always to aim for an OTIF score as close to 100% as possible, which symbolizes optimal operations efficiency.
How Can Businesses Track OTIF Performance?
Now that you know how to calculate OTIF, the next step is tracking the metric effectively to optimize your supply chain and improve customer satisfaction. Below are several strategies businesses can employ to monitor their OTIF performance efficiently.
Integrated Software Systems
Leverage ERP (Enterprise Resource Planning) or dedicated supply chain management software with capabilities to track delivery and order fulfillment metrics. These systems automate OTIF calculations by integrating sales, inventory, and logistics data.
Dashboard Reporting
Employ dynamic dashboards that provide real-time visual feedback on OTIF performance. These tools can highlight trends, pinpoint disruptions, and enable managers to make swift, data-driven decisions.
Data Analytics
Regular data analysis should be conducted to investigate the causes of delivery delays or incomplete orders. Understanding these patterns helps anticipate and mitigate future issues, improving OTIF scores.
Collaboration Tools
Streamline communication across all departments involved in the supply chain, from warehousing to customer service. Through robust collaboration platforms, businesses can ensure that any potential issues impacting their OTIF are quickly identified and addressed.
Vendor Scorecards
If your supply chain involves third-party vendors, maintain scorecards to monitor their performance in meeting delivery and quality standards, which directly affects your OTIF score.
What Factors Influence OTIF Scores?
A variety of internal and external factors can influence your OTIF score. Studying these influences can help pinpoint areas for improvement.
- Supplier Performance: Delays from suppliers can disrupt schedules, impacting your ability to fulfill orders on time and in full.
- Inventory Management: Poor inventory oversight can lead to product shortages, directly affecting the “In-Full” part of OTIF.
- Logistics and Distribution: Inefficiencies in routing, transportation delays, and problems with delivery services can jeopardize the “On-Time” component.
- Internal Processes: Inadequate order processing or errors in picking and packing can delay shipments and prevent order completion.
- External Factors: Issues like adverse weather conditions, customs holdups, and other uncontrollable events can significantly impact OTIF performance.
Identifying and addressing these factors allows businesses to refine their logistics and supply chain strategies, helping them consistently meet or exceed customer expectations for delivery and completeness.
How Do I Improve OTIF Scores for My Business?
Enhancing your OTIF scores involves a multifaceted approach, focusing on different supply chain elements and operational efficiencies.
Here's how you can start making substantive improvements:
Streamline Your Supply Chain
Reevaluate your logistics strategies to ensure they are as efficient as possible. This strategy might mean choosing more reliable carrier services, optimizing shipping routes, or investing in technology that improves logistics planning.
Enhance Inventory Accuracy
Maintaining accurate inventory records is crucial. Utilize inventory management systems that provide real-time data to avoid overstocking or stockouts, which can affect your ability to fulfill orders.
Strengthen Supplier Relationships
Work closely with your suppliers to ensure they align with your OTIF objectives. Regular communication and performance reviews can help identify and address issues before they impact your supply chain.
Implement Advanced Forecasting Tools
Use predictive analytics to better forecast demand and adjust your inventory and staffing. This proactive approach can minimize delays and ensure you meet customer expectations.
Focus on Continuous Improvement
Encourage a culture of continuous improvement within your organization. Regular training, feedback loops, and incentive programs can motivate employees to maintain high-performance standards in fulfilling orders accurately and on time.
Regular Audits and Adjustments
Conduct periodic audits of your supply chain processes to ensure you’re following best practices and identify areas for improvement. Adjust your strategies based on audit findings to continuously improve OTIF performance.
How Can Cabrella Help With OTIF?
At Cabrella, we recognize the complexities and challenges that businesses face in managing efficient and reliable supply chains. Our comprehensive suite of logistics services is designed to support and enhance your OTIF performance.
Tailored Shipping Solutions
Our advanced shipping software seamlessly integrates with your existing systems, enabling you to manage high-value logistics effectively. This integration ensures your shipments are well-handled and improves your “On-Time” performance.
Custom Insurance Options
With Cabrella, you gain access to customized insurance solutions that protect against risks associated with shipping and handling. This coverage helps goods reach their destinations intact and supports your “In-Full” metric.
Risk Management Expertise
Our deep understanding of logistics and insurance nuances allows us to provide expert advice on risk mitigation, assist you in navigating potential disruptions in your supply chain, and maintain high OTIF scores.
Proactive Monitoring and Alerts
Cabrella’s state-of-the-art tracking systems provide real-time updates and alerts, enabling you to monitor your shipments at every step and react swiftly to any discrepancies or delays.
Partnering with Cabrella means leveraging our expertise and technology to streamline your operations, boost customer satisfaction, and, ultimately, drive your business success with improved OTIF performance.
Upgrade Your Supply Chain With OTIF
Mastering OTIF is an operational goal and strategic imperative that can define your business's success. With Cabrella by your side, you're equipped to conquer the stringent demands of modern supply chain management. Our tools and expertise are your assets to ensure that every order meets and exceeds expectations.
Embrace the logistics journey with Cabrella, where every shipment is a step toward unparalleled customer satisfaction and operational excellence. Join us in redefining what's possible for your supply chain.
Sources:
What Is On-Time In-Full (OTIF)? | Indeed
What Is A Supply Chain? | CIPS
Enterprise Resource Planning (ERP): Meaning, Components, and Examples | Investopedia
Data Analytics: Definition, Uses, Examples, and More | Coursera
Keep Checking Out Our Other Posts
Subscribe for Email Updates
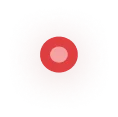