A Close Look at Material Requirement Planning and MRP System
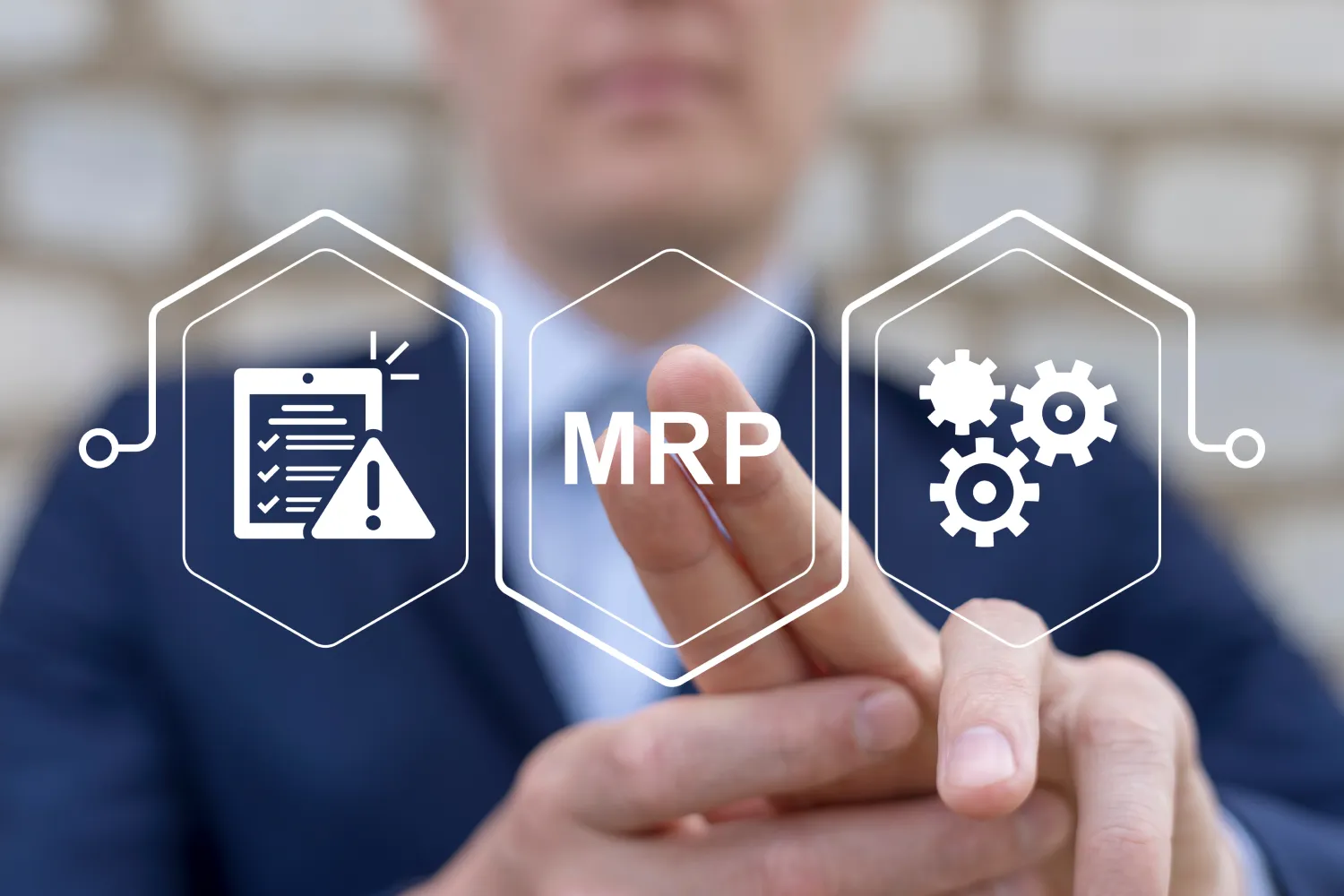
In the bustling world of manufacturing and supply chains, staying ahead means deploying the right tools — and material requirement planning (MRP) systems are exactly that.
At Cabrella, we understand the importance of precision in managing your production and inventory. MRP systems are not just tools but strategic assets that align your operations with market demands, ensuring you manage resources efficiently and keep your production lines moving smoothly. Ready to see how MRP can transform your business?
Let’s take a close look at how these systems streamline operations and drive growth.
What Is Material Requirement Planning (MRP)?
Material requirement planning (MRP) is a systematic approach to managing all resources in a manufacturing process. It starts with a schedule for finished goods that is converted into a list of requirements for the sub-assemblies, component parts, and raw materials needed to produce these goods, all within set time frames.
MRP integrates data from production schedules, inventory records, and bills of materials to calculate exactly what materials are necessary, how much is needed, and when they should be ordered. The concept of MRP first took root in the 1960s as a simple method to determine quantities and timing of material purchases.
It evolved from the basic reorder point systems of the early 20th century and was developed to address the complex planning operations of large-scale manufacturing during and after World War II. By the 1970s, as computer technology became more accessible and cost-effective, MRP systems began to gain a foothold in factories around the world.
This integration of technology allowed for more sophisticated data analysis and real-time updates, revolutionizing how factories managed their inventories and production processes. Today, MRP is integral to supply chain management, serving as the spine that supports various planning activities and ensuring the right materials are available for production at the right time.
Its evolution continues as it adapts to the complexities of modern manufacturing environments, proving crucial for efficiency and effectiveness in meeting consumer demand and managing production costs.
How Do MRP Systems Enhance Operational Efficiency?
MRP systems enhance operational efficiency by providing a comprehensive overview of inventory needs and production scheduling. This visibility ensures that all parts of the manufacturing process are aligned, which helps reduce idle time in production machines and minimize bottlenecks.
With an MRP system, companies can streamline their operations by ensuring that materials are available just in time for production, thus avoiding both overstock and stockouts. This just-in-time approach helps reduce inventory carrying costs, as companies no longer need to store large amounts of raw materials or finished products.
Furthermore, MRP systems allow for better labor allocation, ensuring workers are assigned tasks based on real-time needs, which optimizes labor costs and enhances productivity. Another significant benefit is the system's ability to adapt to changes swiftly.
MRP systems can quickly recalibrate operations to accommodate these changes, whether it's a sudden spike in demand, a delay in material supply, or a shift in production priorities. This agility is key to maintaining uninterrupted operations and meeting customer demands efficiently, enhancing the company's reputation and competitiveness in the market.
What Are the Core Components of an MRP System?
Understanding the core components of an MRP system is essential to leveraging its full potential in streamlining production processes.
These components work together to ensure precise management of manufacturing resources:
- Bill of Materials (BOM): This crucial element lists all the materials, components, and assemblies needed to produce a finished product. It details the quantity of each item and the sequence of assembly, serving as a recipe for production.
- Master Production Schedule (MPS): The MPS is the backbone of any MRP system, outlining what needs to be produced, in what quantities, and when. It syncs production with customer demand, ensuring efficient use of resources and timely delivery of products.
- Inventory Records: Accurate inventory records are vital. They track the quantities of raw materials, work-in-progress, and finished goods. These records help determine material requirements and manage stock levels to prevent both surplus and shortages.
- Purchase Orders: MRP systems generate purchase orders automatically based on material requirements, ensuring the procurement process is timely and quantities match the production needs.
- Work Orders: For manufacturing operations, work orders specify jobs, set schedules for the shop floor, and assign tasks based on the MPS and BOM.
- Demand Forecasting: This component uses historical data and sales forecasts to predict customer demand, guiding the MPS in planning future production requirements.
These elements form a cohesive framework that helps businesses streamline their operations, manage complex production lines, and respond adaptively to market changes. By integrating these components effectively, an MRP system can transform the way a company operates, making it more responsive and agile in a competitive marketplace.
How Does an MRP System Integrate With Other Business Processes?
MRP systems don't operate in isolation. They seamlessly blend into the broader ecosystem of enterprise resource planning (ERP) systems. By linking with other business processes, such as financial accounting, human resources, and customer relationship management, MRP systems create a synchronized environment where information flows smoothly across all departments.
This integration allows for:
- Real-time financial tracking, where procurement costs and production efficiency are directly tied to the financial performance of the company, allowing for immediate budget adjustments and financial forecasting.
- Enhanced customer service by aligning production schedules with customer demand forecasts, thus improving delivery times and responsiveness to market changes.
- Human resources management through more accurate labor planning and scheduling, ensuring that staffing levels are optimized for production needs without unnecessary labor costs.
What Challenges Are Associated With Implementing an MRP System?
Implementing an MRP system can be a transformative move, but it comes with its set of challenges.
The main issues typically include:
Complexity in Integration
Many businesses face difficulties in integrating MRP systems with existing IT infrastructure, especially if legacy systems are deeply entrenched.
Data Accuracy
The effectiveness of an MRP system hinges on the quality of the data it receives. Inaccurate data input concerning inventory levels, supplier lead times, or customer demand can lead to production snags, excess inventory, or stockouts.
Change Management
Employees often resist changes in their working processes. Training and helping staff adapt to a new system can be time-consuming and costly, yet it’s essential for successful implementation.
Cost of Implementation
The upfront costs of purchasing and implementing an MRP system can be significant. Smaller manufacturers may find the cost prohibitive, though the long-term savings and efficiencies usually justify the investment.
How To Choose the Right MRP System for Your Business
When selecting an MRP system, consider scalability to ensure it can evolve with your growing business. The interface should be intuitive, minimizing training time and errors.
Customization is key, as the system should adapt to your unique manufacturing needs. Check for seamless integration with existing software to streamline operations. Evaluate the system’s cost against potential efficiency gains and revenue increases.
Also, consider the vendor's reputation for reliable support and system updates. For businesses managing high-value inventory, partnering with a provider like Cabrella ensures your MRP system is enhanced with top-tier shipping and insurance solutions, integrating smoothly and adding an extra layer of security and efficiency to your logistics operations.
What Future Trends Are Shaping MRP Systems?
MRP systems are continually evolving, integrating cutting-edge technologies to enhance their effectiveness.
Here are some of the key trends shaping the future of MRP systems:
Artificial Intelligence (AI) and Machine Learning (ML)
AI and ML are increasingly being integrated into MRP systems to improve demand forecasting and inventory optimization. These technologies help in predicting market trends more accurately and can dynamically adjust production schedules and material orders based on real-time data.
Internet of Things (IoT)
IoT technology enables real-time tracking of materials and inventory through sensors and connected devices. This integration helps automate inventory management and enhance the accuracy of the data fed into MRP systems.
Cloud Computing
Cloud-based MRP solutions offer flexibility, scalability, and accessibility. They reduce the need for heavy upfront investments in IT infrastructure and enable remote access to the system, which is crucial for modern distributed manufacturing setups.
Sustainability and Circular Economy
Future MRP systems will increasingly focus on sustainability. This includes optimizing material use to reduce waste and planning for recycling and reusing materials as part of a circular economy.
Advanced Analytics and Big Data
Leveraging big data analytics to process large volumes of information can help uncover insights about production processes, enabling continuous improvement and operational excellence.
Customization and Personalization
As businesses seek to differentiate themselves in competitive markets, MRP systems that offer greater customization capabilities in production processes will become more popular. These systems will allow companies to meet specific customer demands more efficiently.
Wrapping Up
Material requirement planning (MRP) is an essential tool that meticulously manages production and inventory in manufacturing. By ensuring efficient use of materials and aligning production with market demand, MRP systems support operational excellence and strategic planning.
Integrating these systems with Cabrella's specialized shipping and insurance solutions can significantly enhance your logistics framework, providing seamless security for high-value shipments.
Ready to elevate your manufacturing efficiency and safeguard your operations? Contact Cabrella today to see how our expert solutions can amplify the benefits of your MRP system, helping you achieve and surpass your operational objectives.
Sources:
Material Requirements Planning (MRP): How It Works, Pros and Cons | Investopedia
The early road to material requirements planning | ScienceDirect
Demand Shock: Definition, Causes, Impact, and Examples | Investopedia
Keep Checking Out Our Other Posts
Subscribe for Email Updates
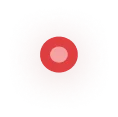